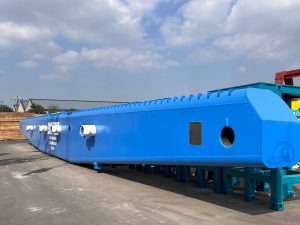
Corrosion Protection Master: How to Choose the Right Epoxy Primer for You?
In the realm of corrosion protection, epoxy primers are renowned for their robust anti-corrosion and rust-prevention properties, earning them the
As the construction machinery market becomes more active, competition among manufacturers extends beyond performance to aesthetics, making the quality of coating on parts particularly important.
De-oiling → Masking → Shot Blasting → Cleaning → Primer Spraying → Drying → Finish Coating → Leveling → Drying → Cooling → Touch-up → Assembly.
Use a towel soaked in de-oiling agent to wipe the surface. The towel should be folded three times to maximize usage; do not ball it up. Wipe in one direction only to avoid secondary contamination. Remove splatters and particles from edges and corners with a scraper. The surface should feel non-greasy after de-oiling.
Remove all loose oxide scale, rust, and coatings. Use rubber plugs, bolts, and special masking tools to cover threaded holes, shaft holes, fit surfaces, and nameplates. Avoid using materials like paper tape that can be knocked off during shot blasting.
3.1 Material Selection: Use alloy steel shot with a diameter of 0.8mm-1.0mm, without adding wire. Ensure the surface roughness is 15-25μm after blasting to avoid excessive coarseness that affects gloss.
3.2 Quality Requirements: At least 9 out of 12 blast heads should exceed 20A, achieving Sa 2.5 cleanliness. The surface should show only slight spot or streak marks and have a metallic sheen.
3.3Pellet and Dust Removal:Use the compressed air pipe and the shot suction machine to clean the steel shot on the structural parts and the inner cavity, blow the floating dust, and finally use the dry ice blasting machine to spray it comprehensively to ensure that the surface cleanliness reaches level 2, see the figure below:
4.1 Paint Adjustment: Check the reliability of the lifting link and clean the viscometer with a solvent before and after measuring. Stir the sample evenly.
4.2 Spraying Technique: Hold the spray gun perpendicular to the surface, 20-30cm away, at a speed of 30-60cm/s with 1/2 to 1/3 overlap. Required coating thickness is 90-130μm. Maintain proper hand, eye, and body posture during spraying.
Dry the primer at 70-80°C for 40-60 minutes and the finish coat at 70-75°C for 50-60 minutes. Confirm actual drying using either the cotton ball method or finger touch method to check for surface residues. Necessary tools include steel shot and sandblasting equipment.
Note: The above content is compiled from online sources. If there are any copyright infringements, please contact us for removal!
As the source manufacturer, Jiangsu Zhongke Sunwell Technology Co, Ltd. have spent 30 years doing a good job in every barrel of paint, and providing industry supporting solutions for free.
Have questions?Reach out to us, and we will provide you with a perfect solution.
In the realm of corrosion protection, epoxy primers are renowned for their robust anti-corrosion and rust-prevention properties, earning them the
As a member of the epoxy paint family, it is one of the most familiar epoxy products, which is widely
Look closely at the three major types of fluorocarbon coating on the market! Fluorocarbon paint generally refers to fluorocarbon paint,
2024 © YaLang All Rights Reserved
Download our catalog to check all of our products and data sheet, select the right coatings for your projects.