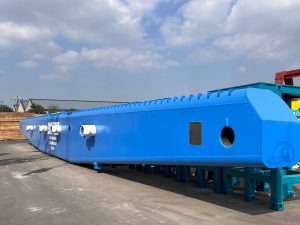
Corrosion Protection Master: How to Choose the Right Epoxy Primer for You?
In the realm of corrosion protection, epoxy primers are renowned for their robust anti-corrosion and rust-prevention properties, earning them the
As the first link in product competition, the coating of engineering machinery products is highly emphasized by all manufacturers. To meet market competition needs, many manufacturers have increased their efforts in technological upgrades to improve coating quality. Compared to internationally renowned brands, domestic engineering machinery products still show significant differences in coating quality. The aesthetic performance of coatings needs further enhancement, particularly in aspects such as coating fullness, smoothness, and gloss. The direct reasons for these differences are the noticeable disparities in the flatness of the workpiece surfaces and differences in coating raw materials. Today, the coating system for engineering machinery has been largely established. Next, we will introduce some choices and processes for engineering machinery paint coatings.
1.Film Thickness:Engineering machinery products generally require coatings to have a certain thickness, necessitating multiple spraying applications.
2.Hardness:One crucial aspect of the coating for engineering machinery products is its high hardness, which must resist impacts and abrasion. Generally, baked coatings are harder than air-dried coatings, so baking processes are preferred in design whenever possible.
3.Adhesion:Adhesion of the coating film is an important indicator of mechanical strength. The key to good adhesion is proper pre-treatment, with shot blasting being the most reliable pre-treatment process. Therefore, structural components of engineering machinery typically use shot blasting methods.
4.Weather Resistance: Since engineering machinery often operates in outdoor environments, weather-resistant coating materials are required.
5.Gloss:The gloss of the coating depends on the fineness of the spray equipment’s atomization. The finer the atomization, the better the gloss. Airless spraying with good atomization should be used whenever possible.
Engineering machinery products vary greatly in type, specification, size, and weight. Different products have different production characteristics and usage environments, leading to distinct coating processes.
– Structural Parts: Shot Blasting (or Sand Blasting) → Cleaning → Primer Application → Drying → Putty Application → Drying → Assembly.
– Complete Machines:Cleaning → Water Spot Drying → Putty Application → Drying → Sanding and Cleaning → Topcoat 1 → Drying → Topcoat 2 → Drying → Finished Product. (Moisture drying and putty drying are mostly air-dried.)
– Structural Parts:
1.Common Process:Shot Blasting → Cleaning → Primer Application → Drying → Putty Application → Sanding and Cleaning → Intermediate Coating → Drying → Topcoat → Drying → Assembly.
2.Latest Process: Shot Blasting → Cleaning → (Degreasing, Phosphating, Pure Water Washing and Spraying) → Moisture Drying → Primer → Solvent Evaporation and Leveling → Topcoat → Leveling → Drying → Assembly.
– Complete Machines: Cleaning → Water Spot Drying → Putty Touch-Up and Bottom Coating → Drying → Finished Product.
The topcoats used for engineering machinery generally include self-drying coatings that can be cured at low temperatures. These coatings include modified alkyd enamel, acrylic engineering enamel, and polyurethane enamel, which meet various customer requirements.
Low-temperature curing is used to improve adhesion and hardness. The topcoat must match the primer, putty, and intermediate coating system. The quality difference in topcoat materials is a major factor affecting domestic and international coating quality, and domestic paint manufacturers need to develop high-quality, cost-effective products to meet local market demands.
The coating production line for structural parts and complete machines of engineering machinery mainly consists of shot blasting cleaning chambers, cleaning chambers, moisture drying chambers, sanding chambers, spray booths, coating drying chambers, finishing rooms, and conveying equipment.
The layout of process equipment is closely related to product characteristics and the coating process used. Factors such as whether the product is wheeled or tracked, the type of putty applied, and the use of intermediate coating processes influence the entire process layout.
The process layout is also closely related to the conveyor system of the production line. Currently, domestic structural part coatings generally use self-propelled hoist conveyors with stacking functions. There are three main types of complete machine coating production lines: double chain conveyors, rail transfer vehicle conveyors, and self-propelled methods. Equipment for these methods is arranged in a flow line layout, with each process completed in separate chambers.
The surface pre-treatment of structural parts uses automatic shot blasting. Shot blasting involves projecting abrasive materials at high speed onto the steel surface to remove oxidation, rust, and other contaminants through impact and abrasion. The shot blasting chamber includes the cleaning chamber body, shot blaster, shot blasting cylinder, spray gun, abrasive recycling system, ventilation and dust collection system, bottom structure, and electrical control system.
(1)The cleaning chamber body generally has the optimal position for installing shot blasters (quantity depends on the blasting volume). The blasters are arranged at an angle to ensure that all parts of the workpiece are cleaned. The chamber doors must remain closed during blasting to prevent abrasive particles from escaping. The chamber’s inner lining is made of high-manganese cast steel plates, which are durable and interchangeable.
(2) A shot blasting cylinder with two spray guns is installed at the chamber’s outlet end. The interior wall is protected with wear-resistant rubber plates to ensure reliability and reduce equipment costs. The chamber’s entrance and exit are equipped with electric doors for automatic or manual control.
The spray booth includes the chamber body, air supply and exhaust systems, lighting system, paint mist treatment system, control system, and flammable gas concentration alarm device.
(1)The upper part of the booth has a static pressure chamber integrated with the booth structure. High-efficiency filter non-woven fabrics are used to supply clean air in laminar flow from the top of the booth, effectively controlling the diffusion of paint mist.
(2)The air supply system needs to include primary and secondary filters, a heating section (with steam as the heat source, ensuring indoor temperatures ≥15°C in winter). Airflow uniformity across all sections is required to avoid mist escape.
(3)The paint mist purification efficiency should exceed 99%. The exhaust system has a gas-water separation device, with treated air being discharged into the atmosphere.
(4)Organic waste gas treatment must meet national air pollution discharge standards. Gas concentration monitoring alarms continuously detect flammable gases, with alarms triggered when solvent concentration reaches 25% of the explosion limit.
The drying chamber uses forced hot air convection circulation. Energy sources include steam, electricity, liquefied gas, and light diesel. The equipment consists of the chamber body, hot air circulation system, and exhaust gas purification equipment. The hot air circulation system typically uses a four-element heating furnace (insert-type fan, fuel heating system, high-temperature filter, and integrated exhaust gas treatment). The heating speed is fast, with uniform indoor temperatures and temperature differences <+5°C.
Note: The above content is compiled from online sources. If there are any copyright infringements, please contact us for removal!
As the source manufacturer, Jiangsu Zhongke Sunwell Technology Co, Ltd. have spent 30 years doing a good job in every barrel of paint, and providing industry supporting solutions for free.
Have questions?Reach out to us, and we will provide you with a perfect solution.
In the realm of corrosion protection, epoxy primers are renowned for their robust anti-corrosion and rust-prevention properties, earning them the
As a member of the epoxy paint family, it is one of the most familiar epoxy products, which is widely
Look closely at the three major types of fluorocarbon coating on the market! Fluorocarbon paint generally refers to fluorocarbon paint,
2024 © YaLang All Rights Reserved
Download our catalog to check all of our products and data sheet, select the right coatings for your projects.