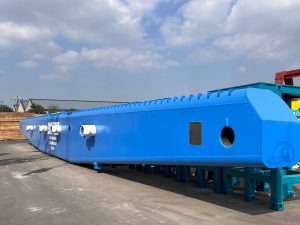
Corrosion Protection Master: How to Choose the Right Epoxy Primer for You?
In the realm of corrosion protection, epoxy primers are renowned for their robust anti-corrosion and rust-prevention properties, earning them the
Waterborne epoxy anti-corrosion coatings refer to coatings with high water resistance that exhibit poor hydrophilicity during application, which prevents water from permeating through and thus ensures effective anti-corrosion performance. With the rapid development of the chemical industry in China, there is increasing emphasis on the production and research of anti-corrosion coatings. By finding suitable material ratios through anti-corrosion design, relevant work can be implemented in anti-corrosion treatments, laying a foundation for the effective implementation of anti-corrosion measures. This paper focuses on the application of additives in waterborne epoxy anti-corrosion coating formulations. The significance of this study lies in analyzing the application of additives in the formulation of waterborne epoxy anti-corrosion coatings based on existing experimental conditions. This ensures that the entire material application configuration is well-established and enhances the anti-corrosion performance of the material.
In line with the requirements for the preparation of waterborne epoxy anti-corrosion coatings, the following materials were selected for experimental analysis: Zinc phosphate (Harbin Jiapeng Petrochemical Co., Ltd.); Modified aluminum phosphate (Harbin Jiapeng Petrochemical Co., Ltd.); Red iron oxide (Beijing New Energy Petrochemical Co., Ltd.); Talcum powder (Harbin Third Talcum Powder Plant); Mica powder (Haicheng Xingxin Talcum Powder Plant); Precipitated barium sulfate (provided by Hongchang Electronic Materials Co., Ltd.); DS-195L (Tianjin Saide Chemical Co., Ltd.).
The experimental instruments selected for this study include the Kruss B-100 Dynamic Surface Tensiometer, a fineness gauge, a 101-type electric hot air drying oven, and a TDL-5A desktop low-speed centrifuge.
Based on the requirements of the selected experimental equipment, a scientific analysis of the reagent preparation process was conducted to ensure improved reagent formulation outcomes. The main reagent information is as follows:
– Zinc phosphate: 2.0% – 5.0%
– Modified aluminum phosphate: 2.0% – 5.0%
– Red iron oxide: 12.0% – 18.0%
– Talcum powder: 3.0% – 5.0%
– Mica powder: 3.0% – 5.0%
– Precipitated barium sulfate: 10.0% – 15.0%
– Dispersant: 0.1% – 0.6%
– Wetting agent: 0.1% – 0.5%
– Defoamer: 0.1% – 0.3%
– Water: 10.0% – 40.0%
– Curing agent: 10.0% – 20.0%
Preparation process:
First, according to the formulation manufacturing requirements, water and dispersant are added to a container, mixed, and stirred evenly. Zinc phosphate, modified aluminum phosphate, red iron oxide, talcum powder, mica powder, and precipitated barium sulfate are then sequentially added.
Next, the mixture is subjected to centrifugal separation at a speed of 2500 – 300 rpm. After grinding into a slurry, the wetting agent, defoamer, and additional water are added, and stirring continues until the waterborne epoxy anti-corrosion coating is obtained.
The prepared experimental materials are tested according to the requirements of existing experimental analyses. Testing focuses on the following four aspects:
(1)Stability test: Based on certain experimental reagents, the mixture is placed in a test tube and subjected to centrifugal separation in a centrifuge, with a separation time of 10 minutes and a centrifuge speed of 2500 – 300 rpm.
(1)Viscosity test: The prepared experimental reagent is stored at 40°C room temperature, and the viscosity is analyzed and recorded periodically.
(3)Dynamic and surface tension test: The reagent is tested for surface tension using the Kruss B-100 Dynamic Surface Tensiometer according to reagent handling requirements.
(4)Fineness test: Fineness measurements are conducted based on a fineness gauge for scientific analysis.
Analysis of the experimental results revealed significant differences in coating stability due to the method of additive addition during reagent preparation. Overall, in the preparation of waterborne epoxy anti-corrosion coatings, the dispersant’s impact on coating stability is based on thermodynamic principles. During preparation, the dispersant’s static ions cause an increasing aggregation of particles, which can reduce the coating’s performance if not controlled effectively. However, the addition and handling of additives provide a foundation for improving waterborne epoxy material anti-corrosion effects and coating stability.
Dispersants also significantly affect coating compatibility. During the preparation of waterborne epoxy anti-corrosion coatings, the addition of dispersants leads to a notable change in the viscosity relationship between materials and additives. Overall, the addition of dispersants improves the performance of waterborne epoxy anti-corrosion coatings. Viscosity analysis shows that the material’s processing performance changes due to dispersant control. Proper adjustment of anti-corrosion agents and additives according to coating treatment requirements is essential for enhancing material performance. Analysis shows that dispersants impact coating viscosity primarily within 5 – 7 days, with viscosity slightly increasing after 5 days and stabilizing after 7 days.
The application of defoamers significantly affects the preparation of waterborne epoxy anti-corrosion coatings. Analyzing the effect of defoamers on experimental reagent preparation shows some impact on the preparation outcomes but significantly improves the coating’s water and corrosion resistance. The addition of defoamers establishes a foundation for improving preparation effectiveness and stabilizing the performance of the experimental reagent.
The application of wetting agents in the preparation of waterborne epoxy anti-corrosion coatings enhances the reagent formulation effectiveness and guides improvements and optimization of reagent treatment effects. When added, wetting agents impact the coating’s water solubility management. The surface tension of the coating shows significant differences, with notable improvements in anti-corrosion performance when surface tension reaches 75.5 mN/m. This indicates that adding wetting agents significantly enhances the coating’s anti-corrosion quality.
In summary, the application of additives in the formulation process of waterborne epoxy anti-corrosion coatings enhances the effectiveness of anti-corrosion material preparation and ensures better coating performance. This study demonstrates that, under current experimental conditions, dispersants have a significant impact on coating stability and compatibility. The effects of defoamers and wetting agents on material surfaces are also notable. The addition of these additives provides a solid foundation for improving the anti-corrosion performance of materials.
Note: The above content is compiled from online sources. If there are any copyright infringements, please contact us for removal!
As the source manufacturer, Jiangsu Zhongke Sunwell Technology Co, Ltd. have spent 30 years doing a good job in every barrel of paint, and providing industry supporting solutions for free.
Have questions?Reach out to us, and we will provide you with a perfect solution.
In the realm of corrosion protection, epoxy primers are renowned for their robust anti-corrosion and rust-prevention properties, earning them the
As a member of the epoxy paint family, it is one of the most familiar epoxy products, which is widely
Look closely at the three major types of fluorocarbon coating on the market! Fluorocarbon paint generally refers to fluorocarbon paint,
2024 © YaLang All Rights Reserved
Download our catalog to check all of our products and data sheet, select the right coatings for your projects.