FRP anti-corrosion
FRP anti-corrosion is a composite material with anti-corrosion, corrosion resistance, acid and alkali resistance, insulation and other properties, and its basic materials are glass fiber reinforced materials and resins.
1. Strong anti-corrosion: As a chemical anti-corrosion material, FRP anti-corrosion has strong anti-corrosion performance, which can prevent the corrosion and oxidation of metal materials and enhance the service life of materials.
2. High durability: Since FRP anti-corrosion is a chemical anti-corrosion material, it will not cause structural deformation, leakage and other problems due to changes in the natural environment, so it has high durability.
3. Convenient construction: Compared with traditional metal materials, FRP does not need special equipment and tools during anti-corrosion construction, and only needs simple manual operation.
4. Light weight and high strength: The density of FRP anti-corrosion is relatively light, but its strength is very high, and it has good compressive performance and impact resistance.
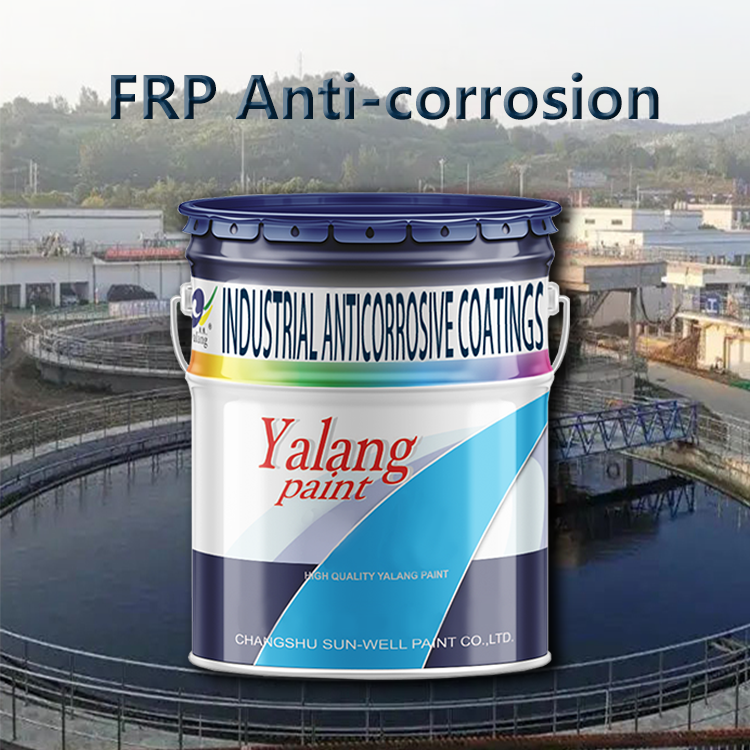
FRP ANTI-CORROSION
REASON FOR SELECTION
SCOPE OF APPLICATION
It is widely used in medicine, chemical industry, machinery, light industry, electronics, power plants, battery factories, electroplating plants, aluminum factories, metallurgical plants and other occupations of acid, alkali and salt resistant workshops, warehouses, storage tanks, walls, ground, sewage treatment tanks and other equipment.
FRP ANTI-CORROSION ENGINEERING
1. Hand lay-up method: lining glass cloth (felt) on the side, and applying adhesive (prepared glue) until the required number of layers (thickness), after curing, it becomes a FRP product.
2. Winding method: After continuously dipping the glass fiber yarn or glass cloth with glue solution, it is continuously wound on the tire mold or lining by hand or machinery, and it becomes a glass fiber reinforced plastic product after curing. It is mainly used in the manufacture of pipes, high-pressure vessels and cylindrical equipment.
3. Molding method: put the glass cloth of the dried impregnated solution into the mold for heating and pressurization, and solidify after a certain period of time.
4. Jetting method: The resin and curing agent are sprayed into fine particles by spraying a spray gun, and mixed with the chopped fibers sprayed by the FRP fiber cutter and sprayed on the surface of the mold, and then cured by rolling.
For example, for equipment that is subject to vapor phase corrosion or weak corrosive liquid media, it is generally enough to line with 3-4 layers of glass cloth. In corrosive environments with harsh conditions, the total thickness of the lining should be at least greater than 3mm. During the lining process, the adhesive must be applied so that each layer of glass cloth is thoroughly soaked to squeeze out as much air as possible from the gaps between the fibers. And it is best to stick one layer per lining, and then paste the next layer after drying or heat treatment, so that the solvent can be fully volatilized and the resin is cured, which is conducive to improving the impermeability of the FRP lining.
The component material of resin anti-corrosion is FRP, which has all the advantages of resin, and the required technical indicators can be achieved through scientific and reasonable material selection, process design and structural design, and the characteristics of FRP anti-corrosion are as follows:
(1) Good designability;
(2) Excellent mechanical properties;
(3) Chemical corrosion resistance;
(4) Good heat and cold resistance;
(5) It has good thermal insulation performance;
(6) The coefficient of thermal expansion is small;
(7) Lightweight, high strength, easy installation;
(8) Excellent electrical insulation performance.
Anti-corrosion liners are unvulcanized, pre-vulcanized, or vulcanized rubber sheets or sheets designed to prevent corrosion of equipment. The technique of forming a continuous insulating covering layer with a lined rubber sheet on the working surface of a metal or other material is called adhesive lining. Lining rubber can be divided into soft rubber, hard rubber, and semi-hard rubber, which is generally manufactured with NR, CR and SBR according to the use conditions. The manufacturing of linings includes the surface treatment of metal substrates, the processing of lining rubber sheets, cutting, lamination and vulcanization. As a chemical anti-corrosion and anti-mechanical wear material, the lining rubber plate is widely used as the lining of chemical equipment and the lining of mud pumps for mining and metallurgy, flotation machines, mills, cement mills for building materials industry and other equipment.
Epoxy resin lining and brushing 901 special resin: epoxy resin and glass fiber cloth are made into an anti-corrosion and waterproof lining, and then a number of 901 special resin coatings are painted. The practice includes one cloth and three oils (also known as one cloth and three coats, one cloth and three glues), two cloths and four oils (coating, glue), three cloths and five oils (coating, glue), four cloths and six oils (coating, glue), five cloths and seven oils (coating, glue), six cloths and eight oils (coating, glue), seven cloth jiu oil (coating, glue), eight cloth and ten oils (coating, glue), nine cloth and eleven oils (coating, glue), ten cloth and twelve oils (coating, glue), etc. (and so on, oil, coating, glue are two more times than cloth)