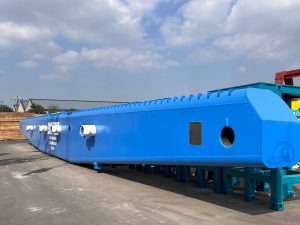
Corrosion Protection Master: How to Choose the Right Epoxy Primer for You?
In the realm of corrosion protection, epoxy primers are renowned for their robust anti-corrosion and rust-prevention properties, earning them the
The main base material of coatings is polymer materials, which often experience discoloration, softening, adhesion failure, blistering, and even cracking in the presence of water. Therefore, water resistance is a critical aspect of coating performance.
1.Discoloration
The resin or color generates chromophores under the influence of water.
2.Softening
Water causes swelling and plasticization of the coating, leading to reduced strength and hardness.
3.Adhesion Failure
Water molecules replace the interfacial interactions (including some hydrogen bonds or easily hydrolyzed chemical bonds) between the coating and the substrate, greatly reducing adhesion.
4.Blistering
Due to softening and adhesion failure, evaporating water can lift the coating.
In essence, the effects of water on coatings can be summarized into two aspects:
1.High water absorption, leading to dampness (or slow drying, making complete drying difficult).
2.The coating is prone to various physical and chemical interactions with water that degrade its performance (such as containing easily hydrolyzed ester or ether bonds).
1.Chemical Affinity
Hydrophilic groups in the coating adsorb water molecules onto their polar surfaces through cationic coordination or hydrogen bonding, resulting in a certain degree of water absorption (generally dominated by chemical adsorption after film formation).
2.Capillary Action
Commonly observed in the water absorption of porous materials, this is a form of physical adsorption. The material itself must have a certain degree of hydrophilicity, such as diatomaceous earth, especially if the coating has incomplete degassing channels during drying.
3.Osmotic Action
If electrolytes are present in the coating, osmotic pressure can cause water from outside to penetrate inside the coating. However, when cohesive energy within the coating is significant, it can partially counteract this osmotic pressure.
Resins with good water resistance should have the following characteristics:
– High hydroxyl value
– Low acid value
– High glass transition temperature (minimal flexible chain alcohol)
– High molecular weight and narrow molecular weight distribution
– Minimal polar monomers
– Monomers with urea or amine groups that enhance wet adhesion
– Suitable salt-forming agents
The most commonly used is HDI aliphatic isocyanate trimer. Previously, polyether chain-end modification was common, but the residual polyether segments in the film significantly reduce water resistance. It’s better to use HDI modified with sulfonates, which, after drying, leaves behind minimal sulfonate groups that degrade water resistance much less than polyether-modified HDI.
Be cautious with hydrophilic swelling silicate fillers, such as montmorillonite and kaolin. Additionally, metal ions in montmorillonite can destabilize dispersions; if necessary, use volatile amine modifications. For talc and precipitated barium sulfate, choose those that have undergone hydrophobic treatment. Pay attention to the chemical structure, charge, and surfactants used in organic colorants. Coating hydrophobicity can also be enhanced by adding nanomaterials, particularly nano-silica.
Limit the use of additives rich in hydrophilic groups. It is particularly important to highlight cosolvents (or film-forming aids) that have high boiling points and evaporate slowly, as they can remain in the film long after drying and reduce water resistance.
Select high hydroxyl value resin dispersions and appropriate catalysts to ensure high crosslinking density after curing. Research indicates that increasing the amount of curing agent appropriately can enhance water resistance (the best NCO/-OH ratio is between 1.5 and 2.0). However, too much curing agent can be counterproductive and reduce water resistance. High crosslinking density requires complete reaction of the crosslinking agents; otherwise, excessive hydroxyl groups can accumulate. Additionally, excessively high crosslinking density can deteriorate impact and bending properties. Thus, an optimal crosslinking state for resins is a balanced crosslinking density with a thorough reaction extent.
Reducing the surface tension of the coating can enhance its hydrophobicity.
Waterborne coatings dry slowly, and residual water may remain in the film long after application, which can degrade performance before complete drying. The coating must resist damage from this residual water, referred to as “initial water resistance,” which is closely related to application techniques. After complete drying (with extremely low water content), long-term use may still pose a risk of moisture absorption due to hydrophilic structures, necessitating assurance of “long-term water resistance.”
Note: The above content is compiled from online sources. If there are any copyright infringements, please contact us for removal!
As the source manufacturer, Jiangsu Zhongke Sunwell Technology Co, Ltd. have spent 30 years doing a good job in every barrel of paint, and providing industry supporting solutions for free.
Have questions?Reach out to us, and we will provide you with a perfect solution.
In the realm of corrosion protection, epoxy primers are renowned for their robust anti-corrosion and rust-prevention properties, earning them the
As a member of the epoxy paint family, it is one of the most familiar epoxy products, which is widely
Look closely at the three major types of fluorocarbon coating on the market! Fluorocarbon paint generally refers to fluorocarbon paint,
2024 © YaLang All Rights Reserved
Download our catalog to check all of our products and data sheet, select the right coatings for your projects.