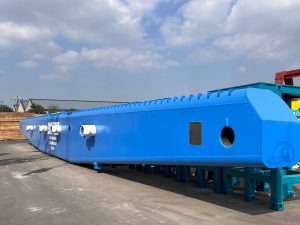
Corrosion Protection Master: How to Choose the Right Epoxy Primer for You?
In the realm of corrosion protection, epoxy primers are renowned for their robust anti-corrosion and rust-prevention properties, earning them the
Given the frequent quality and safety incidents in the petroleum industry over recent years, which have negatively impacted the national economy, as well as the inadequacies in corrosion protection and insulation technology affecting the service life of pipelines, tanks, and equipment, it is essential to improve and elevate the quality of corrosion protection and insulation construction.
1.Corrosion protection for the upper surface of the bottom plate inside the oil tank, involving sandblasting and rust removal.
2.Corrosion protection for the inner surface of the tank wall, involving sandblasting and rust removal.
3.Corrosion protection for the underside of the floating roof tank, involving sandblasting and rust removal.
4.Corrosion protection for the internal surfaces of the floating roof tank, involving sandblasting and rust removal.
5.Corrosion protection for the surface of the central drainage pipe inside the tank, involving sandblasting and rust removal.
6.Corrosion protection for the underside of the central sump inside the tank, involving sandblasting and rust removal.
7.Corrosion protection for the accessories such as the central drainage pipe supports and wax scraping board supports, involving sandblasting and rust removal.
1.Sandblasting and rust removal for the exposed surfaces of the floating roof and tank body.
2.Rust removal and corrosion protection for the internal surfaces of the floating roof.
3.Rust removal and corrosion protection for the tank’s upper platform, steps, floating ladders, and reinforcing rings.
4.Manual rust removal and corrosion protection for the tank’s spray piping and fire protection piping.
5.Rust removal and corrosion protection for all external valves of the tank.
6.Sandblasting and rust removal for the outer wall of the tank.
7.Sandblasting and rust removal for the underside of the tank’s bottom plate.
8.Corrosion protection for the external insulation supports and accessories, involving sandblasting and rust removal.
The outer bottom plate of the tank is in direct contact with the tank foundation. It requires a coating combined with cathodic protection using external current. The environment demands coatings with good water resistance and durability, and since cathodic protection is used, good resistance to cathodic delamination is also required. Considering cost-effectiveness and technical maturity, epoxy and polyurethane coatings are recommended for this area.
The corrosive environment is a typical industrial atmospheric corrosion environment. The requirements for the coating system under this environment include:
1.Good rust resistance;
2.Good adhesion and mechanical properties such as impact resistance;
3.Excellent UV resistance and color retention;
4.Good application performance to adapt to on-site conditions;
5.Reliable technology with high cost-effectiveness.
Currently, the most widely used coating system is: epoxy zinc-rich primer/epoxy micaceous iron intermediate coat/acrylic polyurethane finish.
This area is typically the most severely corroded part of crude oil storage tanks. The corrosive medium mainly consists of crude oil and sediment water, which has a complex composition. The corrosion characteristics in this area include electrochemical corrosion with severe localized corrosion and pitting, which can easily lead to perforation. It is recommended to use heavy-duty epoxy anti-corrosion coatings combined with sacrificial anode cathodic protection. Water-based lithium silicate zinc-rich coatings can be applied to the tank bottom, providing cathodic protection and being environmentally friendly and easy to apply.
Cleaning the metal surface of the tank is one of the most important steps in corrosion protection construction, directly affecting the adhesion of the coating. Currently, the common method in the industry for cleaning the metal surface of storage tanks is open sandblasting. However, this method has several issues: high labor intensity for workers, significant dust pollution affecting health, and environmental pollution that does not meet eco-friendly requirements, leading to its gradual elimination. The more advanced metal surface cleaning process in use is steel plate shot blasting. The process involves: first, surface pretreatment of the steel plates, followed by the application of primer and rolled plates; after completing the tank construction, the surfaces of weld seams are cleaned and re-primed, and finally, intermediate and finish coats are sprayed over the entire tank.
1.Coating Application Method:High-pressure airless spray is used for application, following these steps:
– First: Spray the first coat of primer on the cleaned steel plates.
– Second: Perform arc pre-forming on the steel plates; after pre-forming, apply the remaining primer and one coat of intermediate paint.
– Third: Assemble and install the tank plates, followed by cleaning and touch-up of weld seams.
– Finally: Spray the finish coat on the entire tank.
2.Coating Quality Control:
The effectiveness of corrosion protection largely depends on coating quality. The influencing factors and their impact levels are as follows: surface treatment quality (50% influence); film thickness (20% influence); pre-coating and other factors (30% influence). Therefore, during the coating process, it is crucial to strictly adhere to the technical conditions specified in the paint instructions, with special attention to the following three aspects:
(a)Surface Treatment:
Surface treatment is the primary factor affecting the service life of the paint film. It is essential to control surface cleanliness to meet specified requirements and to manage surface roughness, as any poorly treated surface will hinder the corrosion protection performance of the coating.
(b) Film Thickness:
The thickness of the paint film is also a significant factor in its corrosion resistance. Thickness checks should be performed using a magnetic thickness gauge. Measurement of dry film thickness should ideally be completed before full curing to allow for repairs to any areas that are too thin. If a large area of the film is below standard, re-coating will be challenging.
The dry film thickness should follow the “90-10” principle: 90% of the measured points must meet the specified thickness, while the remaining 10% must be within 90% of the specified thickness, with local film thickness not exceeding 200%.
(c) Pre-Coating:
Since corrosion often occurs first at welds and joints, special attention should be given to these areas during coating. They should be brushed first before applying the full coat to ensure effective corrosion protection.
The specific steps for constructing the insulation layer are:
1.Clean the tank’s outer surface to remove dirt and oil, ensuring the surface is dry.
2.The insulation layer construction must comply with regulatory requirements as well as national policies.
3.The insulation layer should be installed using a bundling method, ensuring it fits tightly against the container surface and is secured with galvanized wire.
4.The insulation layer should be arranged in a staggered pattern.
In conclusion, to ensure the long-term use of crude oil storage tanks and to reduce corrosion and economic losses while achieving safe and civilized production, it is recommended to implement online corrosion monitoring and enhance technical economic analysis to make corrosion protection efforts more detailed and effective.
Note: The above content is compiled from online sources. If there are any copyright infringements, please contact us for removal!
As the source manufacturer, Jiangsu Zhongke Sunwell Technology Co, Ltd. have spent 30 years doing a good job in every barrel of paint, and providing industry supporting solutions for free.
Have questions?Reach out to us, and we will provide you with a perfect solution.
In the realm of corrosion protection, epoxy primers are renowned for their robust anti-corrosion and rust-prevention properties, earning them the
As a member of the epoxy paint family, it is one of the most familiar epoxy products, which is widely
Look closely at the three major types of fluorocarbon coating on the market! Fluorocarbon paint generally refers to fluorocarbon paint,
2024 © YaLang All Rights Reserved
Download our catalog to check all of our products and data sheet, select the right coatings for your projects.