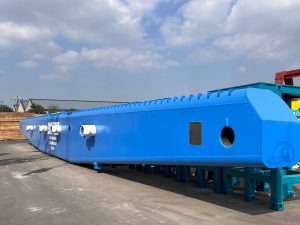
Corrosion Protection Master: How to Choose the Right Epoxy Primer for You?
In the realm of corrosion protection, epoxy primers are renowned for their robust anti-corrosion and rust-prevention properties, earning them the
With the development of society and the improvement of aesthetic standards, users have higher demands not only for the performance of construction machinery but also for its appearance quality. In recent years, the export volume of construction machinery products has significantly increased, prompting manufacturers to focus on surface quality to close the gap with similar products abroad and enhance competitiveness in international markets. The choice of coatings and their application are critical to achieving the desired appearance quality for construction machinery products.
1.Minimal permeability to water, oxygen, and corrosive agents.
2.Strong and durable adhesion to the substrate.
3.Good rust prevention and decorative properties.
4.Special features such as insulation, conductivity, and heat resistance.
5.An appropriate coating system.
With the needs for industrial energy conservation and environmental protection, coatings should also have low-temperature quick-drying and eco-friendly energy-saving properties, particularly suitable for painting smaller batches of construction machinery components and whole machines. Currently, domestic construction machinery typically uses epoxy ester primers and polyurethane topcoats. The former has good rust prevention properties, while the latter offers good decorative qualities.
Acrylic latex paint generally consists of acrylic emulsions, pigments, water, and additives. It has moderate cost, excellent weather resistance, good adjustability, and does not release organic solvents, making it a rapidly developing type of coating. It is primarily used for interior and exterior walls of buildings, leather coatings, etc. New varieties like wood latex paint and self-crosslinking latex paint have recently emerged. Acrylic latex paints can be categorized based on the emulsion used, including pure acrylic, styrene-acrylic, silicone-acrylic, and vinyl-acrylic.
Solvent-based acrylic paint features excellent weather resistance and high mechanical properties and is currently a rapidly developing coating type. It can be divided into self-drying acrylic paints (thermoplastic) and cross-linking cured acrylic paints (thermosetting). The former is non-conversion coating, while the latter is a conversion type. Self-drying acrylic paints are mainly used for architectural coatings, plastic coatings, electronic coatings, and road marking paints, offering quick surface drying, ease of application, and notable protective and decorative effects. However, their disadvantages include lower solid content, difficulty in balancing hardness and elasticity, and an inability to achieve thick film layers in a single application. Cross-linking cured acrylic paints include varieties such as amino acrylic paints, polyurethane acrylics, and radiation-cured acrylics, and they are widely used in automotive coatings, electrical coatings, wood coatings, and architectural coatings. These types typically have high solid content, allowing for thick film application and excellent mechanical properties, resulting in coatings with high weather resistance, fullness, elasticity, and hardness. The drawbacks include complex two-component systems, more challenging application processes, and requirements for heating or radiation curing, demanding good equipment and skilled application techniques.
Polyurethane coatings are a common type of paint, divided into two-component and single-component formulations. Two-component polyurethane coatings consist of isocyanate prepolymers (also known as low molecular weight amino carbamate polymers) and hydroxyl-containing resins, commonly referred to as curing agents and main agents. This category includes various types and wide applications, categorized based on the hydroxyl components such as acrylic polyurethane, alkyd polyurethane, polyester polyurethane, polyether polyurethane, and epoxy polyurethane. They generally possess good mechanical properties, high solid content, and overall excellent performance. They are promising for applications in wood coatings, automotive refinishing, anti-corrosion coatings, floor coatings, electronic coatings, and specialty coatings. The disadvantages include complex application processes, high environmental requirements, and a tendency for defects in the paint film. Single-component polyurethane paints include varieties like polyurethane oil paints, moisture-cured polyurethane paints, and closed polyurethane paints. Their application scope is narrower than that of two-component paints, mainly used for flooring, anti-corrosion, and pre-coated materials, and their overall performance is less comprehensive than that of two-component variants.
Nitrocellulose paint is a common coating for wood and decoration. It offers good decorative effects, is easy to apply, dries quickly, has low environmental requirements, and exhibits good hardness and gloss with fewer film defects and easy repair. However, its solid content is relatively low, requiring multiple application layers for optimal effects; durability is poor, especially for interior nitrocellulose paints, which can suffer from loss of gloss, cracking, and discoloration over time; and its film protection is inadequate against organic solvents, heat, and corrosion. The main film-forming component is nitrocellulose, combined with alkyd resins, modified rosin resins, acrylic resins, and amino resins. It generally requires the addition of plasticizers such as dibutyl phthalate, dioctyl phthalate, and castor oil. Solvents mainly include esters, ketones, and alcohol ethers, as well as auxiliary solvents like alcohols and diluents like benzene. Nitrocellulose paint is mainly used for wood and furniture coatings, home decoration, general decorative coatings, metal coatings, and standard cement coatings.
Epoxy paint has rapidly developed as an industrial coating in recent years, generally referring to coatings containing a high number of epoxy groups. The main types of epoxy paint are two-component formulations composed of epoxy resin and curing agents. There are also some single-component self-drying varieties, but their performance lags behind that of two-component coatings. The main advantages of epoxy paints include strong adhesion to inorganic materials such as cement and metal, excellent corrosion resistance, good mechanical properties, wear and impact resistance, and the ability to produce solvent-free or high-solid content coatings. They are resistant to organic solvents, heat, and water, and the film is non-toxic. However, their weather resistance is poor, and prolonged exposure to sunlight may lead to chalking, limiting them to use as primers or for indoor applications; they have limited decorative qualities and gloss retention; their application environment is demanding, with slow curing at low temperatures affecting performance; many types require high-temperature curing, which entails significant equipment investment. Epoxy resin coatings are primarily used for floor coatings, automotive primers, metal anti-corrosion, and chemical corrosion protection.
Amino paint consists of two main components: amino resin and hydroxyl resin. The amino resin component includes butyl etherified melamine-formaldehyde resin, methyletherified melamine-formaldehyde resin, and butyl etherified urea-formaldehyde resin. The hydroxyl resin component mainly consists of medium to short oil alkyd resins, hydroxyl-containing acrylic resins, and epoxy resins. Aside from urea-formaldehyde resin paints (commonly known as acid-cured paints) used for wood coatings, most amino paint varieties require heat curing, generally above 100°C, with curing times over 20 minutes. The cured film exhibits excellent properties, with hardness, fullness, gloss, and durability, offering good decorative and protective effects. However, they require high standards for application equipment and are energy-intensive, making them unsuitable for small-scale production. Amino paints are mainly used for automotive topcoats, furniture coatings, home appliance coatings, metal surface coatings, and coatings for instruments and industrial equipment.
Note: The above content is compiled from online sources. If there are any copyright infringements, please contact us for removal!
As the source manufacturer, Jiangsu Zhongke Sunwell Technology Co, Ltd. have spent 30 years doing a good job in every barrel of paint, and providing industry supporting solutions for free.
Have questions?Reach out to us, and we will provide you with a perfect solution.
In the realm of corrosion protection, epoxy primers are renowned for their robust anti-corrosion and rust-prevention properties, earning them the
As a member of the epoxy paint family, it is one of the most familiar epoxy products, which is widely
Look closely at the three major types of fluorocarbon coating on the market! Fluorocarbon paint generally refers to fluorocarbon paint,
2024 © YaLang All Rights Reserved
Download our catalog to check all of our products and data sheet, select the right coatings for your projects.