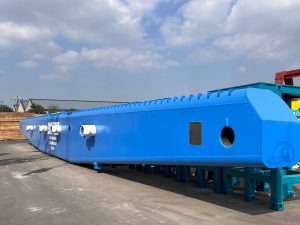
Corrosion Protection Master: How to Choose the Right Epoxy Primer for You?
In the realm of corrosion protection, epoxy primers are renowned for their robust anti-corrosion and rust-prevention properties, earning them the
The decorative, protective, and functional effects of coatings on the surface of coated objects are manifested through the film formed on the object’s surface. The process of forming the desired film on the object’s surface is commonly referred to as coating application or painting. For water-based industrial coatings, application is even more critical. As a product circulating in the market, water-based industrial coatings are essentially semi-finished films; only through application can they form a complete film, thus realizing their intended functions and use value.
The quality of the film directly impacts the decorative effect and use value of the coated object, and this quality is determined by both the coating and the application process. The performance of a coating is often evaluated based on the performance of its film. Poor-quality coatings or non-compliant products will not yield high-quality films. Conversely, high-quality coatings will not achieve excellent performance or the desired decorative or protective effects if the application is improperly executed.
Correct coating application ensures that the performance of the coating is fully reflected in the film. For water-based industrial coatings, the application process is crucial for obtaining a high-quality film and achieving optimal performance.
Pre-surface treatment of the object’s substrate, also known as pre-paint surface treatment, is a fundamental process in coating application. Its purpose is to create optimal conditions for adhesion between the substrate and the film, as well as to enhance and improve the performance of the film.
Steel surfaces often have rust, scale, and oil contamination. Scale, which forms during the high-temperature hot-rolling of steel, has a lower expansion coefficient than steel, is prone to cracking with temperature cycling, and will eventually flake off. Under humid conditions, it forms a corrosion cell where the scale acts as the cathode and the steel as the anode. In this scenario, a large cathode area and a small anode area cause concentrated corrosion pits. Additionally, low oxygen concentration beneath loose scale and high oxygen concentration outside can generate oxygen concentration cells. Therefore, scale must be removed before painting.From a polymer technology perspective, coatings not only form high-molecular films but also serve as good adhesives. Simple plastic films cannot prevent metal corrosion unless they adhere closely to the steel surface. Oil and rust on metal surfaces significantly impact the adhesion and protective performance of coatings, so metal surface treatment must address both rust and oil removal.
To achieve a good anti-corrosion coating, surface treatment is a crucial preparatory step. It is generally believed that the causes for shortened coating lifespan include: poor rust removal quality (40%); inappropriate coating system selection (20%); insufficient coating thickness (20%); improper control of temperature, humidity, and drying time during application (20%).
Steel surface treatment methods can be divided into two categories: mechanical methods, such as sandblasting and chipping, mainly used for thicker steel (over 6mm), such as in ships and port facilities; and chemical methods, such as oil removal, acid dipping, phosphating, and passivation, used for cold-rolled thin steel plates or non-ferrous metals like aluminum and zinc, as well as in automotive, aviation, and home appliances.
Application, also known as coating, painting, or spraying, involves using various methods, tools, and equipment to uniformly apply the coating to the object’s surface. The quality of application directly affects the film’s quality and performance. Different objects and coatings require the most suitable application methods and equipment.
The application methods for water-based industrial coatings generally include brushing, rolling, spraying, and dipping. Factors influencing the choice of application method include investment cost, operating cost, film thickness, appearance requirements, and the structure of the coated object. Reducing VOC (volatile organic compound) emissions drives improvements in application methods. The method impacts the amount of solvent required and solvent recovery. Water, used as the solvent or diluent for water-based industrial coatings, evaporates from the film at a rate that affects the final film’s effect and can also impact the substrate, such as rusting steel or swelling wood fibers.
(1)Brushing: Various brushes can be used, including narrow and wide paintbrushes, long and short-handled brushes, nylon brushes, and polyester brushes. Viscosity is key for brush application. The viscosity of water-based coatings affects the film’s final appearance. If viscosity is too high, too much coating will be carried out of the container; if too low, the coating on the brush will be insufficient. Low viscosity is needed for easy brushing, but if too low, it may result in runs and drips.
Water-based coatings are generally non-Newtonian fluids with certain thixotropic properties. Their leveling performance is slightly worse than that of solvent-based coatings, so brushing is not recommended for high decorative requirements.
(2)Rolling: Rolling refers to the manual application method using rollers. It is the fastest manual application method and is widely used for applying architectural coatings to walls and ceilings. Various rollers and coverings allow for different patterns to be rolled onto the surface.
The viscosity requirements are similar to those for brushing. When applying coatings with rollers, the film may crack as it stretches during rolling, leading to an uneven surface. Some coatings may stretch between rollers, leaving marks if the viscosity is not controlled for proper leveling.
(3)Spraying: Water-based coatings are generally suitable for spraying, but they present more significant rheological issues compared to brushing. Thickeners can be used to adjust rheological properties, but the dilution process may cause large changes in rheological properties due to the non-solution nature of water-based coatings.
Water-based industrial coatings dry more slowly, but during spraying, they may dry and coagulate near the spray gun, causing blockages. If the coating dries too quickly before reaching the object’s surface, it will be difficult to form a continuous film.
The atomization of the coating during spraying is crucial, as it directly affects the coating and film quality. Improving aspects like spraying capability, smoothing the coating, and reducing spraying time and atomization loss can enhance material utilization. Traditional spraying uses compressed air with pressures of 0.6 to 0.8 MPa. The atomization level depends on the coating-to-air weight ratio, with increased air flow and reduced coating viscosity helping to decrease particle size. Overspray during spraying must be collected and disposed of, often through incineration if it cannot be reused.
Many modern applications use high-pressure airless spraying to improve efficiency. In this method, coatings are pressurized and atomized directly, reducing mist and improving film transfer efficiency. It can apply thicker films and higher viscosity coatings but requires higher safety standards due to increased pressure. High-pressure airless spraying is suitable for large areas with general appearance requirements.
When using high-pressure airless spraying for water-based coatings, the coating’s rheological properties must be considered. The coating must be stable under continuous high shear stress from pumping, and air-mixed technology combines airless and air-assisted spraying. This method uses fluid dynamics principles for delivery and atomization, further atomizing the coating with compressed air after leaving the nozzle. This method can handle higher viscosity coatings and produces fine atomization but with less defined outlines.
Each spraying method should be matched to the specific shape and structure of the object, validated through practical use to ensure that the coating meets the required performance and efficiency for factory applications.
(4)Dipping: Dipping is a traditional method of coating application where the object is immersed in the coating liquid and then removed to allow excess coating to drain off before drying to form a film.
The characteristics of dipping include: simplicity of the application process, high production efficiency, and ease of mechanization. Equipment for dipping is simple and suitable for priming objects. The dipping process requires the object to have a simple shape. Objects with deep grooves, blind holes, or irregularities that trap liquid are not suitable. Dipping is selective for coatings that are prone to skinning or settling. Factors affecting the quality of dipped coatings include the viscosity and temperature of the water-based industrial coating. Viscosity affects the coating thickness and the rate at which excess coating drains off. Lower viscosity speeds up the drainage, while too low viscosity can lead to a thin film. Temperature affects viscosity and should be adjusted to meet the desired requirements. However, higher temperatures cause faster solvent evaporation. For dipping, the ideal temperature range is 20-30°C. Additionally, using a coating with high coverage capability often improves the thin film’s coverage.
The hanging and transport of objects also affect coating quality. To ensure even coating, the best hanging position is with the largest surface area of the object close to vertical and other surfaces at an angle to the horizontal. The object should be prevented from trapping air bubbles during immersion. The object should maintain the same position during excess coating removal and drying.
Dipping methods are categorized into intermittent and continuous based on the object’s dimensions and production volume. Intermittent equipment is fixed for small-batch production, using rotating arms or single-track conveyors. Continuous dipping uses common, suspended chain, or push-rod conveyors for large-batch production.
During the coating process, it is generally not recommended to add new paint or stir. Adding paint or stirring can create bubbles that affect film quality, so periodic stirring is advised. After stirring or adding new paint, allow some time for bubbles to dissipate before proceeding with dipping.
This process involves curing the coating applied to the object’s surface (wet film) into a solid, continuous dry film to achieve the decorative effect.
Note: The above content is compiled from online sources. If there are any copyright infringements, please contact us for removal!
As the source manufacturer, Jiangsu Zhongke Sunwell Technology Co, Ltd. have spent 30 years doing a good job in every barrel of paint, and providing industry supporting solutions for free.
Have questions?Reach out to us, and we will provide you with a perfect solution.
In the realm of corrosion protection, epoxy primers are renowned for their robust anti-corrosion and rust-prevention properties, earning them the
As a member of the epoxy paint family, it is one of the most familiar epoxy products, which is widely
Look closely at the three major types of fluorocarbon coating on the market! Fluorocarbon paint generally refers to fluorocarbon paint,
2024 © YaLang All Rights Reserved
Download our catalog to check all of our products and data sheet, select the right coatings for your projects.