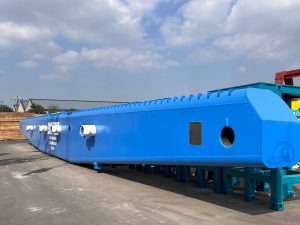
Corrosion Protection Master: How to Choose the Right Epoxy Primer for You?
In the realm of corrosion protection, epoxy primers are renowned for their robust anti-corrosion and rust-prevention properties, earning them the
Mechanical paint, as the name suggests, refers to the paint applied to machinery and equipment. Also known as mechanical coatings, these are applied to the surfaces of machinery and various machine parts. They are mainly used for surface decoration and protection on machine tools, equipment, automobiles, hardware, fiberglass, and more. Let’s examine the technical requirements of the coating process and methods to improve coating adhesion.
Mechanical products generally require a thick coating film. To achieve a certain thickness, multiple coats are necessary. For a film thickness of less than 20μm, low-pressure spraying is used; for a film thickness of 20-40μm, medium-pressure spraying is employed; and for a thickness over 40μm, high-pressure spraying is required.
For mechanical products, the most crucial aspect of the coating is its ability to withstand impact and abrasion, which means high mechanical strength is essential. To achieve ideal strength, the coating film needs to be thick, hard, and have good adhesion. The hardness of the film depends on the quality of the paint and the ideal baking effect. Typically, baked coatings are harder than air-dried coatings, so baking processes are commonly used in design.
Adhesion is a key indicator of mechanical strength. The quality of pre-treatment is central to adhesion. For structural parts of engineering machinery, shot blasting is generally used, followed by dust blowing, pre-treatment phosphating, and primer application. The goal is to achieve optimal adhesion of the coating film. The choice of spraying method also affects adhesion. Higher spray speeds (kinetic energy) and the presence of static electricity (electrostatic energy) can enhance adhesion.
Engineering machinery products are used outdoors, so good weather resistance is required. The coating film should be able to resist corrosion and withstand harsh outdoor conditions while ensuring even application and avoiding pinholes and bubbles.
Gloss depends entirely on the finesse of atomization. Finer atomization results in better gloss. Gloss is a direct reflection of surface aesthetics. While engineering machinery does not require gloss as high as that of automotive finishes, surface appearance still reflects product quality. To achieve an ideal gloss while meeting other technical specifications, an air-assisted airless spray method is recommended for better atomization.
(1)Mechanical Interlocking: Roughening the substrate can enhance adhesion.
(2)Penetration Adhesion: Interaction between coating molecules and substrate molecules through penetration.
(3)Electrostatic Attraction
(4)Intermolecular Forces
Coating Issues:
The adhesion of coatings is directly related to the formulation and quality of raw materials. Poor formulation ratios and raw material quality lead to easy peeling of the coating film.
Application Issues:
(1)Dirty Substrate: Presence of grease or other contaminants that have not been removed.
(2)Incompatibility of Primer with Substrate: The substrate may be too smooth or have low surface energy.
(3)Excessive Moisture or Salt Crystallization: High moisture content or salt deposits on the substrate.
(4)Severe Substrate Powdering or Dust: Powdered substrate or dust not removed after sanding.
Coating Issues:
Improve the uniformity of rigid particle distribution in the coating film and provide appropriate ventilation gaps to enhance adhesion.
(1)Clean the Substrate: Ensure the substrate is dry, clean, and solid. Remove all affected paint films that have lost adhesion, and clean the surface thoroughly before applying new paint.
(2)For Powdered Substrates: Use a suitable high-penetration primer to seal the substrate.
(3)Apply a Waterproof Layer: Ensure the substrate is adequately protected with a waterproof layer to prevent moisture from damaging the coating film.
Note: The above content is compiled from online sources. If there are any copyright infringements, please contact us for removal!
As the source manufacturer, Jiangsu Zhongke Sunwell Technology Co, Ltd. have spent 30 years doing a good job in every barrel of paint, and providing industry supporting solutions for free.
Have questions?Reach out to us, and we will provide you with a perfect solution.
In the realm of corrosion protection, epoxy primers are renowned for their robust anti-corrosion and rust-prevention properties, earning them the
As a member of the epoxy paint family, it is one of the most familiar epoxy products, which is widely
Look closely at the three major types of fluorocarbon coating on the market! Fluorocarbon paint generally refers to fluorocarbon paint,
2024 © YaLang All Rights Reserved
Download our catalog to check all of our products and data sheet, select the right coatings for your projects.