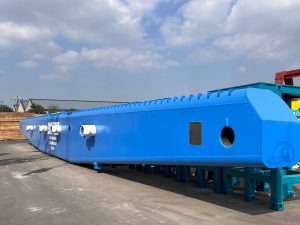
Corrosion Protection Master: How to Choose the Right Epoxy Primer for You?
In the realm of corrosion protection, epoxy primers are renowned for their robust anti-corrosion and rust-prevention properties, earning them the
Historically, construction machinery focused primarily on corrosion resistance, with less emphasis on appearance and decoration. However, as consumer expectations have evolved, there is now a higher demand for the visual quality of these machines. It is essential not only to focus on the internal performance and reliability of the equipment but also to ensure excellent exterior aesthetic performance.
Construction machinery typically features complex structures with many edges and recesses, making it challenging to achieve high aesthetic quality on all surfaces. The coating process is generally divided into two categories:
-Covering Parts Coating: These components require high aesthetic quality and must have excellent corrosion resistance and decorative features.
– Structural Parts Coating: These parts have lower visual quality requirements and focus primarily on corrosion resistance.
Powder coating for construction machinery must not only have good mechanical and corrosion resistance but also exhibit high coating appearance quality, gloss, and appearance brightness (DOI value) as shown below:
NO. | Indicator Item | Quality Requirement |
1 | Paint Film Appearance | Surface should be full, bright, smooth, and defect-free |
2 | Gloss (G60°%) | Directly affects A/B surface, final gloss ≥80% (mainstream manufacturers ≥90%) |
3 | Film Thickness | Above 120μm |
4 | Film Hardness | ≥H |
5 | Adhesion | (Cross-cut test) 0~1 level |
6 | Mechanical Properties | Impact strength (≥50kg·cm), flexibility 2-3mm |
7 | Weather Resistance | Mainstream manufacturers ≥8-10 years |
8 | Salt Spray Resistance | Mainstream manufacturers ≥1000h |
9 | Water Resistance | 240h without visible bubbling, wrinkling, or peeling |
10 | Acid-Base | Resistance (5%) 168h, no discoloration, bubbling, or peeling |
From the performance indicators, it can be seen that the typical film thickness is over 120μm, gloss can reach over 90%, and both salt spray and aging requirements are high. The mechanical and corrosion resistance properties can match those of solvent-based or water-based coatings.
Powder coating technology is straightforward and facilitates automated spraying with robots, offering high efficiency and good coating quality. It can meet high, medium, and low technical requirements. However, large area and edge corner coatings may differ significantly, leading to defects such as thin edges and exposed areas in recesses.
Powder coating generally employs electrostatic powder spraying technology. To effectively address the “edge effect,” a two-coat, one-bake “dry-on-dry” process is often used, combining highly weather-resistant topcoat powder with pure epoxy primer. This approach achieves high decoration and corrosion resistance while providing good edge coverage and hiding capability.
Powder coating requires a clean substrate surface, free from dust, oil, particles, and oxidation. Before coating, ensure the structural parts have good appearance quality, such as straight edges after cutting and smooth, aesthetically pleasing welds. Additionally, improve substrate surface roughness and incorporate degreasing and silane treatment processes to ensure surface cleanliness, enhance paint-substrate adhesion, and improve film quality and performance.
The most challenging aspect of powder spraying is covering edges. The process involves spraying both internal and external edges. While external edges (convex angles) generally have better powder application, melting during baking can lead to thinning of the powder at these edges. Internal edges (concave angles), especially those with cavities or recesses, face issues like the Faraday cage effect in electrostatic spraying, resulting in poor adhesion and localized missing or thin spots. These issues can be addressed with special charging methods to minimize the edge effect, ensuring that the base powder does not float and the top powder covers it effectively.
For structural components made from medium-thick plates, which are complex and vary in thickness, a significant amount of heat is required to achieve curing temperatures. Traditional hot air circulation methods are slow, energy-intensive, and occupy large spaces. Alternatively, using only infrared heating offers uneven temperature distribution, with edges potentially not reaching the desired temperature, affecting coating quality.
Large structural components typically use a combination of infrared radiation and hot air circulation heating. This involves a two-stage process: the first stage uses infrared radiation for 15 minutes, followed by 15 minutes of hot air circulation for temperature maintenance; the second stage involves 15 minutes of hot air circulation for heating, followed by 15 minutes of temperature maintenance until the coating cures. This approach shortens drying time and ensures uniform temperature distribution.
Powder coating processes are relatively streamlined, reducing potential issues and focusing on key quality control steps, including pretreatment, electrostatic spraying, and baking.
Pretreatment effectively removes all types of contaminants from metal surfaces, enhancing corrosion resistance. For simpler shapes with less stringent coating quality requirements, a spray-based treatment process can be used, including degreasing, water washing, fresh water washing, silane treatment, and automated air blowing. Key factors include setting process parameters and chemical dosing accurately. Online analysis and automatic control systems can help monitor tank liquids, dosing, and intelligent control.
For large flat box parts or long tubes, automated spraying with robots or reciprocators is suitable, improving film quality and consistency while reducing labor intensity and avoiding defects such as uneven thickness or missed spots that occur with manual spraying.
A 3D laser profile scanning system can detect the contour of parts, automatically adjust the spray gun distance, and enhance spraying efficiency and uniformity. The control system can simulate the robot’s spraying path based on part shape, eliminating the need for programming and increasing automation efficiency.
Traditional contact coating thickness gauges are only suitable for measuring cured coating thickness and cannot monitor thickness during production. This limitation prevents early detection of quality defects, requiring batch rework if issues arise. A 3D imaging detection technology provides real-time, non-contact measurement of complex parts’ coating thickness distribution, effectively avoiding coating defects and suitable for automated production lines. It also records production data and ensures full traceability.
Excessive temperature during curing can cause overbaking and discoloration, while too low a temperature prevents complete curing, leading to reduced hardness and adhesion issues. The drying chamber temperature can be automatically controlled according to set values, with display and over-temperature alarms. A three-point temperature measurement system in the oven provides a comprehensive view of the curing process, preventing overbaking or poor curing.
The intelligent logistics system incorporates automated logistics recognition and handling technology. For structural part handling, it uses gantry robots, heavy-duty AGV/RGV carts, and automated lifting fixtures. After coating, parts are transported directly to automated storage via an EMS system. The automated logistics system integrates AGV/RGV with robots and chain conveyors to efficiently connect pre-assembly and final assembly stages, achieving efficient, planned production and improved productivity.
In the planning of powder coating production lines for construction machinery, both the initial process design and equipment selection incorporate new technologies and concepts. This approach saves labor and improves coating quality.
(1)Process Design:The application and development trends in construction machinery coating involve using environmentally friendly coating processes. Evaluate factors such as part characteristics, quality requirements, national environmental policies, and overall coating costs to select easily automated processes that enhance efficiency and quality.
(2)Equipment Planning:Due to the variety of construction machinery products, the layout should follow principles of product shape and weight similarity. Consider line flexibility and efficiency while addressing process integration issues to ensure smooth and efficient logistics with minimal crossovers.
Note: The above content is compiled from online sources. If there are any copyright infringements, please contact us for removal!
As the source manufacturer, Jiangsu Zhongke Sunwell Technology Co, Ltd. have spent 30 years doing a good job in every barrel of paint, and providing industry supporting solutions for free.
Have questions?Reach out to us, and we will provide you with a perfect solution.
In the realm of corrosion protection, epoxy primers are renowned for their robust anti-corrosion and rust-prevention properties, earning them the
As a member of the epoxy paint family, it is one of the most familiar epoxy products, which is widely
Look closely at the three major types of fluorocarbon coating on the market! Fluorocarbon paint generally refers to fluorocarbon paint,
2024 © YaLang All Rights Reserved
Download our catalog to check all of our products and data sheet, select the right coatings for your projects.